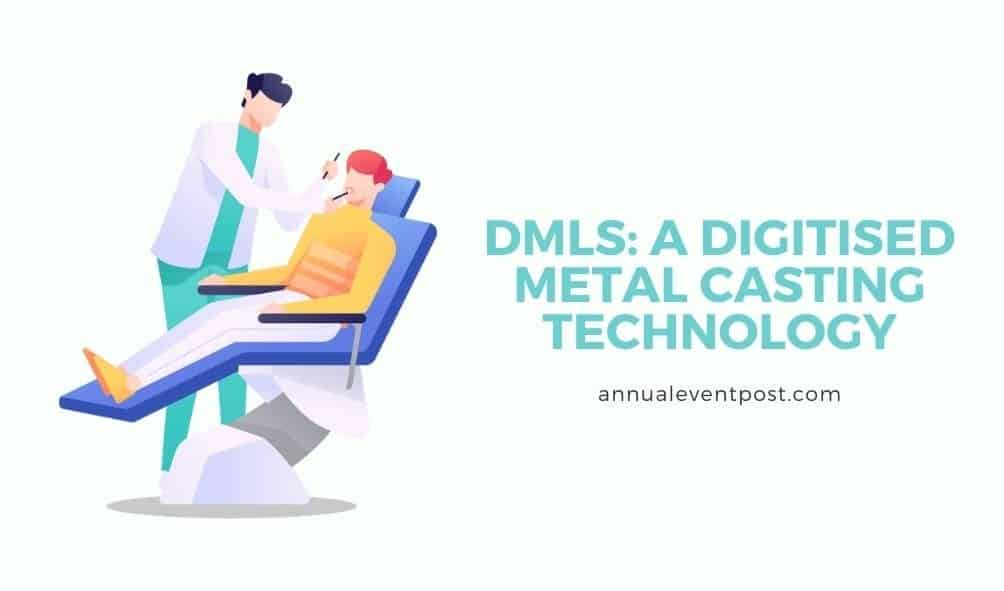
Dental innovation is going through headways at a high speed and innovation is being imported from different fields. One such imported innovation is the Direct Metal Laser Sintering (DMLS) innovation for projecting metal crowns. Laser sintering is the most up-to-date innovation in metal assembling. DMLS is an assembling cycle for creating complex 3D segments straightforwardly from 3D CAD information without utilizing any machining. DLMS requires three data sources: material, energy, and Emax CAD model. The material utilized is powder-based working material. DMLS crowns have an essential synthesis of chrome cobalt combination. Molybdenum, tungsten, silicon, cerium, iron, manganese, and carbon are different fixings utilized. This article will talk about the cycle of laser sintering for making metal crowns and fixed fractional false teeth with a comprehension of their advantages and disadvantages.
What is Direct Metal Laser Sintering (DMLS)
Direct metal laser sintering, or DMLS, is an added substance producing measure whereby a 200-Watt Ytterbium (Yb) fiber-optic laser gets across a bed of powdered metal softening or welding the metal in exceptionally thin layers (about 200um) as indicated by the form convention. After each set layer, a recoater sharp edge uniformly circulates new powder across the forming stage until the whole form record (STL File) is finished. The interaction has a high goal and great surface detail. The utilization of DMLS in dentistry has considered the production of solid and strong scaffolds, crowns, halfway false teeth, and dental prosthetics. Such gadgets are regularly made of cobalt chrome and can be uniquely designed for the patient by following a model of the patient’s dentition and oral life systems. Direct metal laser sintering has been found to create dental prosthetics with both long-haul strength and toughness. A likely weakness to DMLS is the significant expense that is related to the production of prosthetics.
Process of Direct Metal Laser Sintering (DLMS)
- In the dental lab, an impression of a tooth arrangement is made, to begin with, after routine conclusion and treatment arranging. The impression could be conventional or advanced. In the intermediate dental lab, the impression is cast and a model is arranged. The model is checked, and the crown/bridge is planned to utilize a CAD plan and shipped off the focal handling unit. The focal handling unit is generally a distantly found lab with the laser sintering hardware. Extraordinary CAM programming is utilized to import a CAD record, normally provided in the STL design from a scanner/CAD programming. CAM programming further cuts the parts into discrete flat layers.
- Once there are adequate quantities of crown copings and bridge framework (normally 90–120 units) for a task parcel, the laser begins creation layer by layer in a time of a couple of hours. Metal powder is spread across the functioning stage. A powerful laser bar is utilized to dissolve a bed of metal amalgam powder by following a foreordained way layer by layer. This way is made by a CAD document. The machine creates a few hundred dental prostheses out of metal powder. The speed is around 3 min/crown.
- The DMLS measure is performed by two unique strategies, powder deposition, and powder bed strategy; they vary in the manner in which each layer of powder is applied. The powder bed strategy is more mainstream by and by, as they offer quicker paces. Inside the form chamber territory, there are two stages, the material administering stage and the construct stage. The material apportioning stage alongside a re-coater sharp edge is utilized to move new powder over the forming stage. The metal powder is melded into a strong part by softening it utilizing the engaged laser bar. Parts are developed additively layer by layer, normally 20 μm thick. After a layer is assembled the form cylinder brings down the forming stage and the following layer of powder is applied. This interaction considers profoundly complex calculations to be made straightforwardly from the 3D CAD information, completely consequently with no devices, delivering leaves behind higher precision and nitty-gritty goal, great surface quality, and phenomenal mechanical properties. At last, the help material is cut off from the copings/crowns/bridges.
Conclusion
Laser sintering is generally new; makers guarantee that the method is not difficult to utilize, produce precise reclamations, worked on post handling strategies, are liberated from porosity dissimilar to ordinary castings, and improved electromechanical qualities. In any case, further long-haul concentrates on the fit and properties of laser-sintered crowns and fixed dental prostheses, if empowering, could bring about their broad clinical use. The quick headways in the digitalized cycles will keep, making this modernized method more practical. More examination will empower this method to turn out to be more cutthroat.
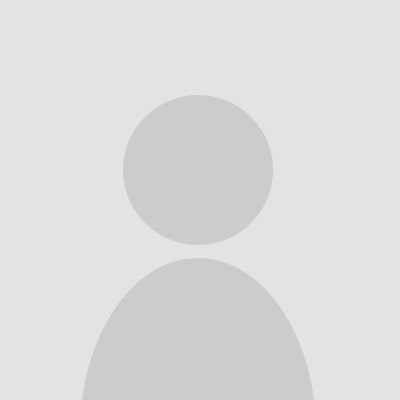
Dr. Ruba just completed her MBBS and she loves to share health tips and write about health-related topics. All the content on this blog related to health is properly researched and practiced by DR Ruba.
Hi! I know this is kind of off topic but I was
wondering which blog platform are you using for this site?
I’m getting tired of WordPress because I’ve had problems with hackers and I’m looking at alternatives for
another platform. I would be fantastic if you
could point me in the direction of a good platform.