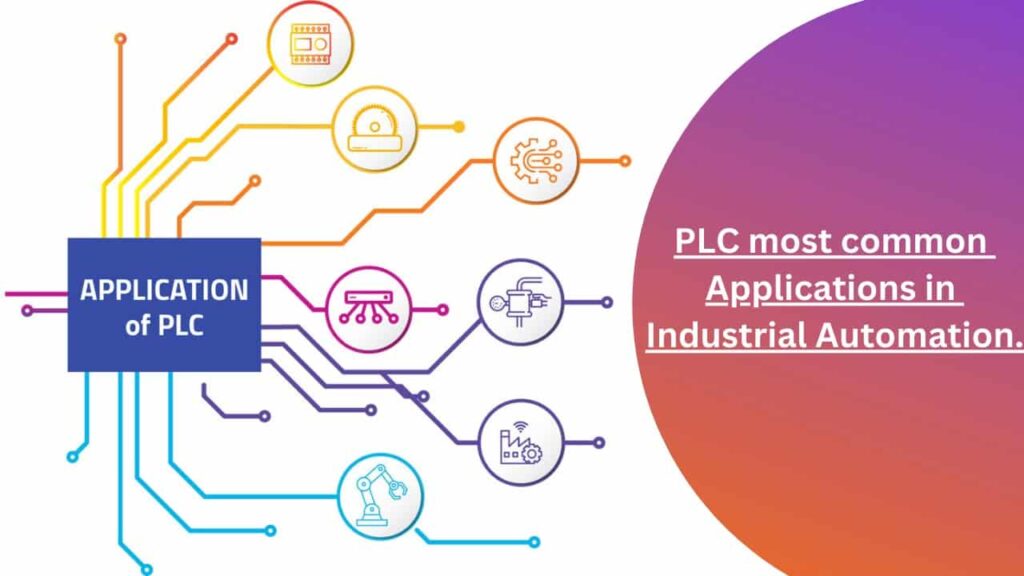
Programmable logic controllers, or PLCs, have grown to be a crucial component of contemporary industrial automation systems. We will examine some of the PLCs’ most widespread uses in industrial automation, where they are used to monitor and operate a variety of industrial processes in place of conventional relay-based control systems.
1. Factory automation:
1766-L32AWA MicroLogix 1400 PLCs are frequently used to manage and monitor a variety of processes in factory automation systems, including assembly lines, conveyor belts, and packing equipment. They are employed to regulate machine speed, keep an eye on product quality, and make sure the equipment is operating well.
The term “factory automation” refers to the use of machinery and technology in a production facility to carry out operations that were previously done by human personnel. This could involve a variety of procedures, including assembly, packaging, quality assurance, and material handling.
These tasks can be automated to increase consistency and quality while decreasing expenses and increasing efficiency. By relieving workers from risky or boring duties, it can also increase safety.
Technologies like robots, computerized systems, and artificial intelligence can all be used to automate processes. To build a highly automated and efficient production process, these technologies can be linked with already-existing industrial machinery.
2. Process control:
In order to monitor and manage different industrial processes including chemical production, water treatment, and oil refining, Rockwell Automation PLCs are also employed in process control systems. They are employed to regulate the flow of materials, keep an eye on the process’s temperature and pressure, and make sure that it is operating within safe parameters.
Process control is the use of technology and systems to track and modify a production process so that it runs smoothly and generates goods of the highest quality. The manufacturing process’s numerous parameters, including temperature, pressure, flow rate, and chemical composition, are measured, analyzed, and real-time modifications are made utilizing the results.
Process control is to keep conditions consistent and ideal throughout the manufacturing process, eliminating waste, maximizing uptime, and enhancing product quality. This can be done by utilizing sensors, actuators, controllers, and other automated systems that collaborate to control the process’s numerous characteristics.
Process control is a vital component of contemporary manufacturing, especially in sectors like chemical processing, the manufacturing of food and beverages, and medicines. Manufacturers may increase efficiency, production, and profitability while also maintaining the security and caliber of their goods by putting in place efficient process control systems.
3. Robotics:
PLCs are a crucial component of robotics systems and are used to direct and track the motion of robots in commercial tasks including material handling, welding, and painting. They are employed to supervise the robots’ positions, manage their speed and direction, and make sure they are working within safe parameters.
Robotics is the study of the creation, maintenance, and use of robots—machines that can do difficult tasks on their own or with little assistance from humans. Robots technology has made considerable strides in recent years, and they are currently utilized in a variety of industries, including manufacturing, healthcare, transportation, and entertainment.
Robots can be programmed to complete specific activities on their own, be directed by a human operator, or function in a hybrid mode where they collaborate with humans. Robots can be made to execute a variety of jobs, from basic ones like moving things around to more difficult ones like putting things together, operating on people, or exploring dangerous situations.
With new developments being made in fields like artificial intelligence, machine learning, and sensor technology, robotics technology is continually developing. This has made it possible to create robots that are more capable, adaptive, and versatile than ever before, and it has created new opportunities for their employees across a variety of sectors and applications.
4. Energy management:
Allen Bradley PLCs are also utilized in energy management systems to track and manage the energy usage of commercial operations. In addition to monitoring the energy usage of various machinery and processes, they are used to manage the lighting, heating, and cooling systems in industrial buildings.
Monitoring, regulating, and conserving energy usage in a building or facility is the practice of energy management, which aims to cut costs and limit environmental effects. This entails putting a variety of techniques and tools into use to raise energy effectiveness, maximize energy use, and cut waste.
5. Building automation:
Building automation systems (BAS) gather information about a building’s environment and activities using sensors, controls, and other automated technologies. These systems then make changes to various systems in real-time to maintain optimum performance and energy efficiency. These systems may be monitored and managed from one central place and can be tailored to match the unique requirements of a building or facility.
PLCs are frequently used in building automation systems to monitor and operate the numerous systems in a building, including the lighting, security, and HVAC (heating, ventilation, and air conditioning) systems. They are employed to regulate the building’s temperature and humidity, keep an eye on its occupants, and make sure it is secure.

https://gallerydeptofficial.net/
https://www.skoposhomes.com